1、范围:
公路桥梁钢结构防腐涂装技术条件
本标准规定了公路桥梁钢结构防腐涂装的分类、要求、试验方法、检验规则、安全、卫生和环境保护以及验收的要求。
本标准适用于公路桥梁钢结构防腐涂装,其它应用领域的桥梁钢结构或类似条件下的钢结构防腐涂装也可参照执行。
3、分类
3.1 涂层体系保护年限分类
3.1.1 在涂层体系保护年限内,涂层95%以上区域的锈蚀等级不大于IS0 4628规定的Ri2级,无气泡、剥落和开裂现象。
3.1.2按保护年限分为两类:
——普通型,(10~15)年;
——长效型,(15~25)年。
3.2腐蚀环境分类
腐蚀环境分类符合IS012944-2的要求,见附录A。
3.3涂装部位分类
按涂装部位分为六类:
——外表面;
——非封闭环境内表面;
——封闭环境内表面;
——钢桥面;
——干湿交替区和水下区;
——防滑摩擦面;
——附属钢构件,包括防撞护栏、扶手护栏及底座、灯座、泄水管、钢路缘石等。
3.4涂装阶段分类
按涂装阶段分为三类:
——初始涂装:新建桥梁钢结构的初次涂装(包含二年缺陷责任期内的涂装);
——维修涂装:桥梁在其运营全过程中对涂层进行的维修保养;
——重新涂装:彻底的除去旧涂层、重新进行表面处理后,按照完整的涂装规格进行的涂装。
4要求
4.1 涂料供应商与施工单位基本要求
4.1.1涂料供应商基本要求
涂料供应商应获得GB/T19001(IS09001),GB/T24001(IS014001)和GB/T28001 (OHSAS18001)认可证书。具备提供技术服务和履约能力。
4.1.2施工单位、施工人员基本要求
4.1.2.1 施工单位应获得GB/T19001(IS09001),GB/T24001(IS014001)和GB/T28001 (OHSAS18001)认可证书。
4.1.2.2施工单位应具有防腐保温二级及以上资质或国家一级及以上企业,具备保证工程安全、质量的能力。
4.1.2.3施工人员应通过涂装专业培训。关键施工工序(喷砂、喷漆、质检)的施工人员应获得涂装中级工及以上证书。特种作业人员应具备相应资格。
4.2涂层体系要求
4.2.1 涂层体系配套要求
4.2.1.1 按照腐蚀环境、工况条件、防腐年限设计涂层配套体系。
4.2.1.2 较高防腐等级的涂层配套体系也适用于较低防腐等级的涂层配套体系,并可参照较低防腐等级的涂层配套体系设计涂层厚度。Cl和C2腐蚀环境下的涂层配套体系,可参考C3腐蚀环境的涂层配套体系进行设计。
4.2.1.3 涂层配套体系表中未列入车间底漆。一般情况下,所有配套都需要喷涂一道干膜厚度为20 μm~25 μm的车间底漆。
4.2.1.4 按涂装部位列明的涂层配套体系表如下:
a) 外表面一暴露于大气环境中的桥梁钢结构外表面涂层配套体系,普通型见表1,长效型见表2;
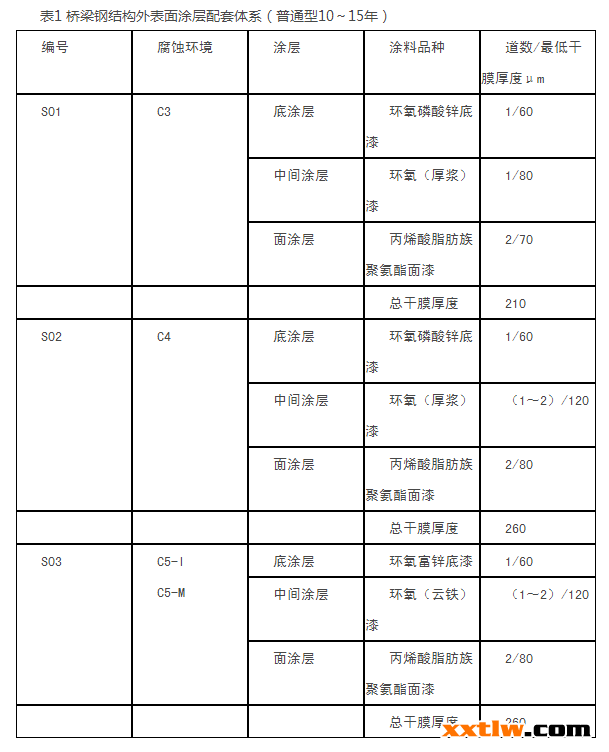
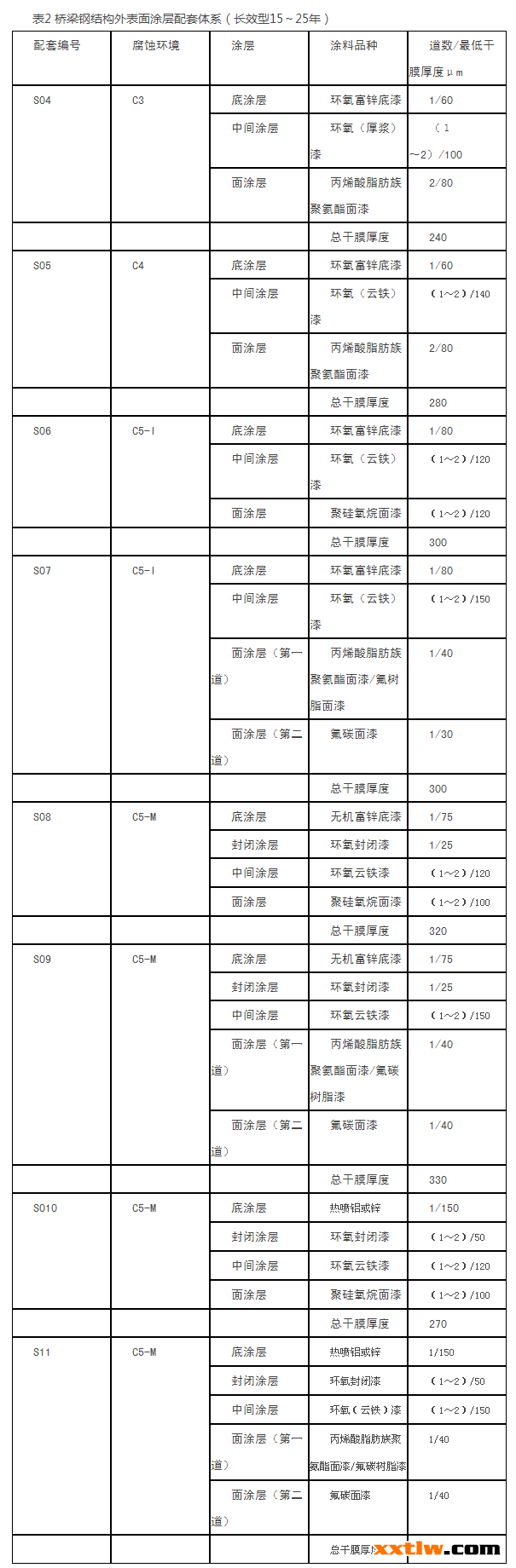
b) 封闭环境内表面涂层配套体系见表3;
表3封闭环境内表面涂层配套体系
S12 配置抽湿机
表3封闭环境内表面涂层配套体系
S12 配置抽湿机
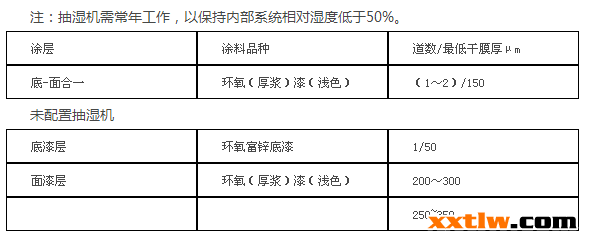
c) 非封闭环境内表面涂层配套体系见表4,或采用与外表面相同的涂层配套体系;
表4非封闭环境内表面涂层配套体系
表4非封闭环境内表面涂层配套体系
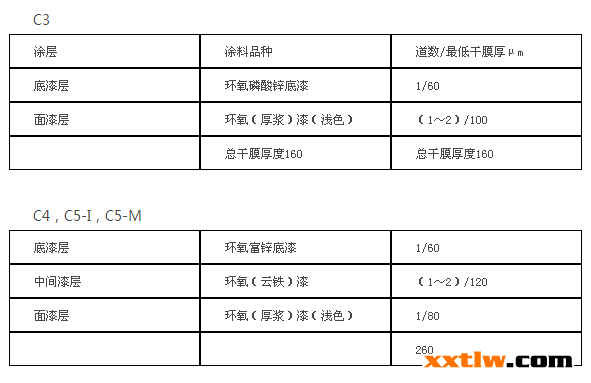
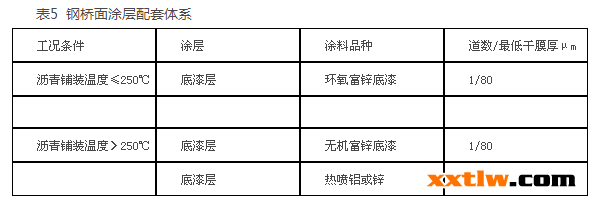
e) 干湿交替区和水下区的涂层配套体系见表6。干湿交替区也可采用钢桥外表面的涂层配套体系,但应适当增加涂层厚度;
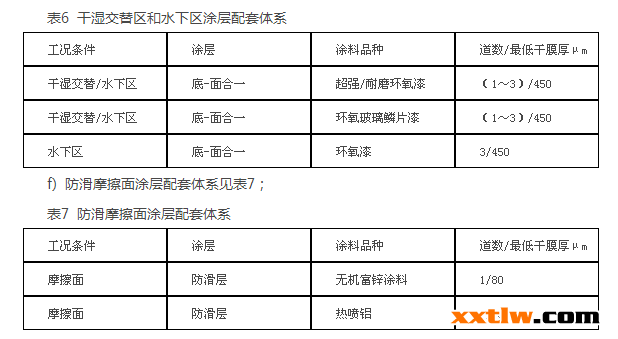
注:热喷铝不适用于相对湿度大、雨水多的环境
g) 附属钢构件可选用表1中的涂层配套体系。
4.2.2涂层体系性能要求
涂层体系性能要求见表8。
表8涂层体系性能要求
g) 附属钢构件可选用表1中的涂层配套体系。
4.2.2涂层体系性能要求
涂层体系性能要求见表8。
表8涂层体系性能要求
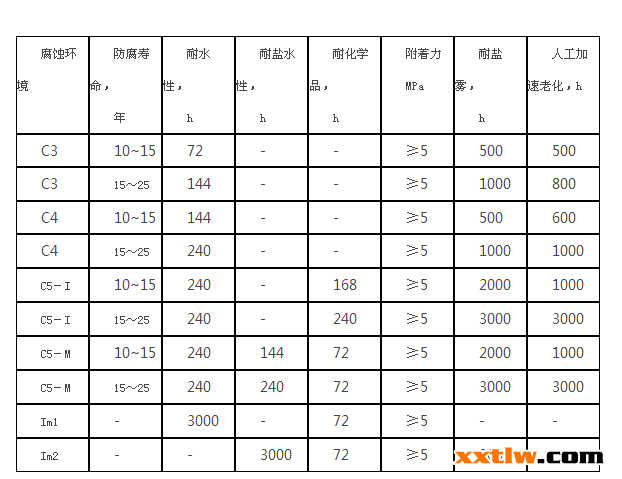
1、耐水性、耐盐水性、耐化学品性能涂层试验后不生锈、不起泡、不开裂、不剥落,允许轻微变色和失光; ┃
2、人工加速老化性能涂层试验后不生锈、不起泡、不剥落、不开裂、不粉化,允许2级变色和2级失光; ┃
3、耐盐雾性涂层试验后不起泡、不剥落、不生锈、不开裂。
4、无机富锌涂层体系附着力大于等于3MPa。
4.2.3涂料性能要求
涂料性能要求见附录B。
4.3工艺要求
4.3.1 表面处理
4.3.1.1 结构预处理
构件在喷砂除锈前应进行必要的结构预处理,包括:
a) 粗糙焊缝打磨光顺,焊接飞溅物用刮刀或砂轮机除去。焊缝上深为0. 8mm以上或宽度小于深度的咬边应补焊处理,并打磨光顺;
b) 锐边用砂轮打磨成曲率半径为2mm的圆角;
c) 切割边的峰谷差超过Imm时,打磨到Imm以下;
d) 表面层叠、裂缝、夹杂物,须打磨处理,必要时补焊。
4.3.1.2 除油
表面油污应采用专用清洁剂进行低压喷洗或软刷刷洗,并用淡水枪冲洗掉所有残余物;或采用碱液、火焰等处理,并用淡水冲洗至中性。小面积油污可采用溶剂擦洗。
4.3.1.3除盐分
喷砂钢材表面可溶性氯化物含量应不大于7 μg/cm2。超标时应采用高压淡水冲洗。当钢材确定不接触氯离子环境时,可不进行表面可溶性盐分检测;当不能完全确定时,应进行首次检测。
4.3.1.4除锈
4.3.1.4.1 磨料要求
a) 喷射清理用金属磨料应符合GB/T 18838.1的要求;
b) 喷射清理用非金属磨料应符合GB/T 17850.1的要求;
c) 根据表面粗糙度要求,选用合适粒度的磨料。
4.3.1.4.2除锈等级为:
a) 热喷锌、喷铝,钢材表面处理应达到GB/T 8923规定的Sa3级;
b) 无机富锌底漆,钢材表面处理应达到GB/T 8923规定的Sa2.5级~Sa3级;
c) 环氧富锌底漆和环氧磷酸锌底漆,钢材表面处理应达到GB/T 8923规定的Sa2'/2级;不便于喷射除锈的部位,手工和动力工具除锈至GB/T 8923规定的St3级。
4.3.1.4.3表面粗糙度为:
a) 热喷锌(铝),钢材表面粗糙度为Rz60 μm~l00 μm;
b) 喷涂无机富锌底漆、,钢材表面粗糙度为Rz50 μm~80 μm;
b) 喷涂其它防护涂层,钢材表面粗糙度为Rz30 μm~75 μm,
4.3.1.4.4除尘
喷砂完工后,除去喷砂残渣,使用真空吸尘器或无油、无水的压缩空气,清理表面灰尘。
7 JT/T 722-2008
清洁后的喷砂表面灰尘清洁度要求不大于GB/T 18570.3规定的3级。
4.3.1.4.5表面处理后涂装的时间限定
一般情况下,涂料或锌、铝涂层最好在表面处理完成后4h内施工于准备涂装的表面上;当所处环境的相对湿度不大于60%时,可以适当延时,但最长不应超过12h;不管停留多长时间,只要表面出现返锈现象,应重新除锈。
4.3.2涂装要求
4.3.2.1 涂装环境要求
施工环境温度5℃~38℃,空气相对湿度不大于85%,并且钢材表面温度大于露点30C;在有雨、雾、雪、大风和较大灰尘的条件下,禁止户外施工。
施工环境温度一5℃~5℃,应采用低温固化产品或采用其它措施。
4.3.2.2涂料配制和使用时间
涂料应充分搅拌均匀后方可施工,推荐采用电动或气动搅拌装置。对于双组分或多组分涂料应先将各组分分别搅拌均匀,再按比例配制并搅拌均匀。
混合好的涂料按照产品说明书的规定熟化。
涂料的使用时间按产品说明书规定的适用期执行。低于5℃施工时,涂料本身的温度需符合产品说明书的规定。
4.3.2.3涂覆工艺
4.3.2.3.1 涂覆方法分为:
a) 大面积喷涂应采用高压无气喷涂施工;
b) 细长、小面积以及复杂形状构件可采用空气喷涂或刷涂施工;
c) 不易喷涂到的部位应采用刷涂法进行预涂装或第一道底漆后补涂。
4.3.2.3.2涂覆间隔
按照设计要求和材料工艺进行底涂、中涂和面涂施工。每道涂层的间隔时间应符合材料供应商的有关技术要求。超过最大重涂间隔时间时,进行拉毛处理后涂装。
4.3.2.3.3二次表面处理
外表面在涂装底漆前应采用喷射方法进行二次表面处理。内表面无机硅酸锌车间底漆基本完好时,可不进行二次表面处理,但要除去表面盐分、油污等,并对焊缝、锈蚀处打磨至GB/T 8923规定的St3级。
4.3.2.3.4连接面涂装法分为:
a) 焊接结构一焊接结构应预留焊接区域。预留区域外壁推荐喷砂除锈至GB/T 8923规定的Sa2.5级,底漆采用环氧富锌涂料,中涂和面涂配套同相邻部位。内壁可进行打磨处理至GB/T8923规定的St3级,采用相邻部位配套进行涂装。
b) 栓接结构:
1)栓接部位采用无机富锌防滑涂料或热喷铝进行底涂。摩擦面涂层初始抗滑移系数不小于0. 55,安装时(6个月内)涂层抗滑移系数不小于0.45。
2)栓接板的搭接缝隙部位,分以下两种情况处理:
一一缝隙小于等于0. 5mm时,采用油漆调制腻子密封处理;
~一缝隙大于0. 5mm时,采用密封胶密封(如聚硫密封胶等);
3)栓接部位外露底涂层、螺栓,涂装前应进行必要的清洁处理。首先对螺栓头部打磨处理,然后刷涂(1-2)道环氧富锌底漆或环氧磷酸锌底漆50 μm--60Um,再按相邻部位的配套体系涂装中间漆和面漆;中间涂层也可采用弹性环氧或弹性聚氨酯涂料。
4.3.2.3.5现场末道面漆涂装前:
a) 应对运输和装配过程中破损处进行修复处理;
b) 应采用淡水、清洗剂等对待涂表面进行必要的清洁处理,除掉表面灰尘和油污等污染物;
c) 应试验涂层相容性和附着力,整个涂装过程要随时注意涂装有无异常。
4.3.3现场涂层质量要求
4.3.3.1 外观
4.3.3.1.1 涂料涂层表面应平整、均匀一致,无漏涂、起泡、裂纹、气孔和返锈等现象,允许轻微桔皮和局部轻微流挂。
4.3.3.1.2金属涂层表面均匀一致,不允许有漏涂、起皮、鼓泡、大熔滴、松散粒子、裂纹和掉块等,允许轻微结疤和起皱。
4.3.3.2厚度
施工中随时检查湿膜厚度以保证干膜厚度满足设计要求。干膜厚度采用“85-15”规则判定,即允许有15%的读数可低于规定值,但每一单独读数不得低于规定值的85%。对于结构主体外表面可采用“90 -10”规则判定。涂层厚度达不到设计要求时,应增加涂装道数,直至合格为止。漆膜厚度测定点的最大值不能超过设计厚度的3倍。
4.3.3.3附着力
4.3.3.3.1 涂料涂层附着力
当检测的涂层厚度不大于250 μm时,各道涂层和涂层体系的附着力按划格法进行,不大于1级;当检测的涂层厚度大于250μm时,附着力试验按拉开法进行,涂层体系附着力不小于3MPa。用于钢桥面的富锌底漆涂层附着力不小于5MPa。
4.3.3.3.2锌、铝涂层附着力
应符合GB/T 9793-1997附录A中A.1.4的规定。
4.4维修涂装和重新涂装
4.4.1 涂膜劣化评定
涂层投入使用后,按照桥梁运行管理单位的规定定期检查,进行涂层劣化评定,评定方法依据IS04628。根据漆膜劣化情况,选择合适的维修或重涂方式。
4.4.2维修涂装
维修涂装要求如下:
a)当面漆出现3级以上粉化,且粉化减薄的厚度大于初始厚度的50%,或由于景观要求时, 彻底清洁面涂层后,涂装与原涂层相容的配套面漆(1~2)道;
b)当涂膜处于(2~3)级开裂,或(2~3)级剥落,或(2~3)级起泡,但底涂层完好时,选择相应的中间漆、面漆,进行维修涂装;
c)当涂膜发生Ri2~Ri3锈蚀时,彻底清洁表面,涂装相应中间漆、面漆。
4.4.3重新涂装
重新涂装要求如下:
a)当涂膜发生Ri3以上锈蚀时,彻底的表面处理后涂装相应配套涂层;
b)当涂膜处于3级以上开裂,或3级以上剥落,或3级以上起泡时,如果损坏贯穿整个涂层,
应进行彻底的表面处理后,涂装相应配套涂层。
4.4.4工艺要点
4.4.4.1 根据损坏的面积大小,钢桥外表面可分为以下三种重涂方式:
a)小面积维修涂装。先清理损坏区域周围松散的涂层,延伸至未损坏区域50mm~80mm,并应修成坡口,表面处理至Sa2级或St3级,涂装低表面处理环氧涂料十面漆;
b)中等面积维修涂装。表面处理至Sa2.5级,涂装环氧富锌底漆+环氧(云铁)漆十面漆;
c)整体重新涂装。表面处理至Sa2.5级,按照4.2.1要求的涂装体系进行涂装。
4.4.4.2钢桥内表面维修或重新涂装底漆宜采用适用于低表面处理的环氧底漆,并宜采用浅色高固体分或无溶剂环氧涂料。
4.4.4.3海洋大气腐蚀环境和工业大气腐蚀环境下的旧涂层须采用高压淡水清洁后,再喷砂除锈。
4.4.4.4处于干湿交替区的钢构件,在水位变动情况下涂装时,应选择表面容忍性好的涂料,并能适应潮湿涂装环境的涂层体系;
4.4.4.5处于水下区的钢构件在浸水状态下施工时应选择可水下施工、水下固化的涂层体系。
5试验方法
5.1涂层配套体系
5.1.1耐水性按GB/T 1733的规定进行。
5.1.2耐盐水性按GB/T 9274的规定进行。
5.1.3耐化学品性能按GB/T 9274的规定进行,使用溶液为5%NaOH和5%H2SO.,水溶液。
5.1.4 附着力按GB/T 5210的规定进行。
5.1.5耐盐雾性能按GB/T 1771的规定进行。
5.1.6人工加速老化性能按GB/T 1865的规定进行。
5.1.7涂层体系试验后,漆膜表面缺陷评判按GB/T 1766的规定进行。
5.1.8涂料的试验方法见附录B。
5.2表面处理
5.2.1 除锈等级评判按照GB/T 8923的规定进行。
5.2.2表面粗糙度按照GB/T 13288或GB/T 10610的规定进行。
5.2.3表面油污检查可采用以下两种方法:
a) 粉笔试验法一一适用于非光滑的钢结构表面
对于怀疑有油污污染的区域,用粉笔划一条直线贯穿油污区域。如果在该区域内,粉笔线条变细或变浅,说明该区域可能被油污污染;
b) 醇溶液试验法一一适用于所有钢结构表面
对于怀疑有油污污染的部位,用蘸有异丙醇的脱脂棉球擦拭,并将异丙醇挤入透明的玻璃管中。加入2~3倍的蒸馏水,振荡混合约20min。以相同体积的异丙醇蒸馏水溶液为参照,如果溶液呈混浊状,表明钢结构表面有油污污染。
5.2.4表面灰尘清洁度按GB/T 18570.3的规定进行。
5.2.5表面可溶性氯化物按GB/T 18570.6和GB/T 18570.9的规定进行。
5.3现场涂层
5.3.1 涂层厚度
5.3.1.1 湿膜厚度按GB/T 13452.2的方法6规定进行。
5.3.1.2干膜厚度按GB/T 13452.2的方法5规定进行。
5.3.2涂层附着力
5.3.2.1 涂料涂层附着力按GB/T 9286或GB/T 5210的规定进行。
5.3.2.2锌、铝涂层附着力按GB/T 9793-1997附录A中的栅格试验法规定进行。
6检验规则
6.1 取样
6.1.1 现场取样应使用专用的样品取样罐。确保现场取样罐的清洁,没有灰尘、水等杂质。
10 JT/T 722-2008
6.1.2抽检的产品包装完整,标志清晰。
6.1.3采用电动或气动搅拌装置,确保抽检产品均匀一致。
6.2检验项目
6.2.1涂层性能的检测项目见表8。
6.2.2进场涂料检测项目由监理、施工方及涂料供应商从附录B中所列项目中选定。
6.2.3现场涂层检测项目按照4.3.3执行。
6.3判定原则
6.3.1 涂层性能的检测为型式检验,应由涂料供应商提供国家认可检测机构出具的涂层性能的合格的检测报告。
6.3.2进场涂料检测结果全部符合本标准的要求为合格。检测结果有一项指标不符合要求时,允许对不符合要求的项目进行复验,复验结果仍不符合要求,则判该批产品为不合格。
6.3.3现场涂层检测结果全部符合4.3.3条款为合格。检测结果有一项指标不符合要求时,都应在现场处理至合格后方可进入下道工序。
7安全、卫生和环境保护
7.1 安全、卫生
7.1.1 涂装作业安全、卫生应符合GB 6514、GB/T 7691、GB/T 7692和GB/T 50212的有关规定。
7.1.2涂装作业场所空气中有害物质不超过最高容许浓度。
7.1.3施工现场应远离火源,不允许堆放易燃、易爆和有毒物品。
7.1.4涂料仓库及施工现场场有消防水源、灭火器和消防工器具,并应定期检查。消防道路应畅通。
7.1.5密闭空间涂装作业应使用防爆灯、器具,安装防爆报警装置;作业完成后油漆在空气中的挥发物消散前,严禁电焊修补作业。
7.1.6施工人员应正确穿戴工作服、口罩、防护镜等劳动保护用品。
7.1.7所有电器设备应绝缘良好,临时电线应选用胶皮线,工作结束后应切断电源。
7.1.8工作平台的搭建应符合有关安全规定。高空作业人员应具备高空作业资格。
7.2环境保护
7.2.1 涂料产品的有机挥发物含量(VOC)应符合国家有关法律法规要求。
7.2.2保持施工现场清洁,产生的垃圾等应及时收集并妥善处理。
8验收
8.1 涂层验收可按构件分批次验收。
8.2涂装承包商至少应提交下列验收资料:
——设计文件或设计变更文件;
——涂料出厂合格证和质量检验文件,进场验收记录;
——钢结构表面处理和检验记录;
——涂装施工记录(包括施工过程中对重大技术问题和其它质量检验问题处理记录);
——修补和返工记录;
——其它涉及涂层质量的相关记录。
附录A(规范性附录)
2、人工加速老化性能涂层试验后不生锈、不起泡、不剥落、不开裂、不粉化,允许2级变色和2级失光; ┃
3、耐盐雾性涂层试验后不起泡、不剥落、不生锈、不开裂。
4、无机富锌涂层体系附着力大于等于3MPa。
4.2.3涂料性能要求
涂料性能要求见附录B。
4.3工艺要求
4.3.1 表面处理
4.3.1.1 结构预处理
构件在喷砂除锈前应进行必要的结构预处理,包括:
a) 粗糙焊缝打磨光顺,焊接飞溅物用刮刀或砂轮机除去。焊缝上深为0. 8mm以上或宽度小于深度的咬边应补焊处理,并打磨光顺;
b) 锐边用砂轮打磨成曲率半径为2mm的圆角;
c) 切割边的峰谷差超过Imm时,打磨到Imm以下;
d) 表面层叠、裂缝、夹杂物,须打磨处理,必要时补焊。
4.3.1.2 除油
表面油污应采用专用清洁剂进行低压喷洗或软刷刷洗,并用淡水枪冲洗掉所有残余物;或采用碱液、火焰等处理,并用淡水冲洗至中性。小面积油污可采用溶剂擦洗。
4.3.1.3除盐分
喷砂钢材表面可溶性氯化物含量应不大于7 μg/cm2。超标时应采用高压淡水冲洗。当钢材确定不接触氯离子环境时,可不进行表面可溶性盐分检测;当不能完全确定时,应进行首次检测。
4.3.1.4除锈
4.3.1.4.1 磨料要求
a) 喷射清理用金属磨料应符合GB/T 18838.1的要求;
b) 喷射清理用非金属磨料应符合GB/T 17850.1的要求;
c) 根据表面粗糙度要求,选用合适粒度的磨料。
4.3.1.4.2除锈等级为:
a) 热喷锌、喷铝,钢材表面处理应达到GB/T 8923规定的Sa3级;
b) 无机富锌底漆,钢材表面处理应达到GB/T 8923规定的Sa2.5级~Sa3级;
c) 环氧富锌底漆和环氧磷酸锌底漆,钢材表面处理应达到GB/T 8923规定的Sa2'/2级;不便于喷射除锈的部位,手工和动力工具除锈至GB/T 8923规定的St3级。
4.3.1.4.3表面粗糙度为:
a) 热喷锌(铝),钢材表面粗糙度为Rz60 μm~l00 μm;
b) 喷涂无机富锌底漆、,钢材表面粗糙度为Rz50 μm~80 μm;
b) 喷涂其它防护涂层,钢材表面粗糙度为Rz30 μm~75 μm,
4.3.1.4.4除尘
喷砂完工后,除去喷砂残渣,使用真空吸尘器或无油、无水的压缩空气,清理表面灰尘。
7 JT/T 722-2008
清洁后的喷砂表面灰尘清洁度要求不大于GB/T 18570.3规定的3级。
4.3.1.4.5表面处理后涂装的时间限定
一般情况下,涂料或锌、铝涂层最好在表面处理完成后4h内施工于准备涂装的表面上;当所处环境的相对湿度不大于60%时,可以适当延时,但最长不应超过12h;不管停留多长时间,只要表面出现返锈现象,应重新除锈。
4.3.2涂装要求
4.3.2.1 涂装环境要求
施工环境温度5℃~38℃,空气相对湿度不大于85%,并且钢材表面温度大于露点30C;在有雨、雾、雪、大风和较大灰尘的条件下,禁止户外施工。
施工环境温度一5℃~5℃,应采用低温固化产品或采用其它措施。
4.3.2.2涂料配制和使用时间
涂料应充分搅拌均匀后方可施工,推荐采用电动或气动搅拌装置。对于双组分或多组分涂料应先将各组分分别搅拌均匀,再按比例配制并搅拌均匀。
混合好的涂料按照产品说明书的规定熟化。
涂料的使用时间按产品说明书规定的适用期执行。低于5℃施工时,涂料本身的温度需符合产品说明书的规定。
4.3.2.3涂覆工艺
4.3.2.3.1 涂覆方法分为:
a) 大面积喷涂应采用高压无气喷涂施工;
b) 细长、小面积以及复杂形状构件可采用空气喷涂或刷涂施工;
c) 不易喷涂到的部位应采用刷涂法进行预涂装或第一道底漆后补涂。
4.3.2.3.2涂覆间隔
按照设计要求和材料工艺进行底涂、中涂和面涂施工。每道涂层的间隔时间应符合材料供应商的有关技术要求。超过最大重涂间隔时间时,进行拉毛处理后涂装。
4.3.2.3.3二次表面处理
外表面在涂装底漆前应采用喷射方法进行二次表面处理。内表面无机硅酸锌车间底漆基本完好时,可不进行二次表面处理,但要除去表面盐分、油污等,并对焊缝、锈蚀处打磨至GB/T 8923规定的St3级。
4.3.2.3.4连接面涂装法分为:
a) 焊接结构一焊接结构应预留焊接区域。预留区域外壁推荐喷砂除锈至GB/T 8923规定的Sa2.5级,底漆采用环氧富锌涂料,中涂和面涂配套同相邻部位。内壁可进行打磨处理至GB/T8923规定的St3级,采用相邻部位配套进行涂装。
b) 栓接结构:
1)栓接部位采用无机富锌防滑涂料或热喷铝进行底涂。摩擦面涂层初始抗滑移系数不小于0. 55,安装时(6个月内)涂层抗滑移系数不小于0.45。
2)栓接板的搭接缝隙部位,分以下两种情况处理:
一一缝隙小于等于0. 5mm时,采用油漆调制腻子密封处理;
~一缝隙大于0. 5mm时,采用密封胶密封(如聚硫密封胶等);
3)栓接部位外露底涂层、螺栓,涂装前应进行必要的清洁处理。首先对螺栓头部打磨处理,然后刷涂(1-2)道环氧富锌底漆或环氧磷酸锌底漆50 μm--60Um,再按相邻部位的配套体系涂装中间漆和面漆;中间涂层也可采用弹性环氧或弹性聚氨酯涂料。
4.3.2.3.5现场末道面漆涂装前:
a) 应对运输和装配过程中破损处进行修复处理;
b) 应采用淡水、清洗剂等对待涂表面进行必要的清洁处理,除掉表面灰尘和油污等污染物;
c) 应试验涂层相容性和附着力,整个涂装过程要随时注意涂装有无异常。
4.3.3现场涂层质量要求
4.3.3.1 外观
4.3.3.1.1 涂料涂层表面应平整、均匀一致,无漏涂、起泡、裂纹、气孔和返锈等现象,允许轻微桔皮和局部轻微流挂。
4.3.3.1.2金属涂层表面均匀一致,不允许有漏涂、起皮、鼓泡、大熔滴、松散粒子、裂纹和掉块等,允许轻微结疤和起皱。
4.3.3.2厚度
施工中随时检查湿膜厚度以保证干膜厚度满足设计要求。干膜厚度采用“85-15”规则判定,即允许有15%的读数可低于规定值,但每一单独读数不得低于规定值的85%。对于结构主体外表面可采用“90 -10”规则判定。涂层厚度达不到设计要求时,应增加涂装道数,直至合格为止。漆膜厚度测定点的最大值不能超过设计厚度的3倍。
4.3.3.3附着力
4.3.3.3.1 涂料涂层附着力
当检测的涂层厚度不大于250 μm时,各道涂层和涂层体系的附着力按划格法进行,不大于1级;当检测的涂层厚度大于250μm时,附着力试验按拉开法进行,涂层体系附着力不小于3MPa。用于钢桥面的富锌底漆涂层附着力不小于5MPa。
4.3.3.3.2锌、铝涂层附着力
应符合GB/T 9793-1997附录A中A.1.4的规定。
4.4维修涂装和重新涂装
4.4.1 涂膜劣化评定
涂层投入使用后,按照桥梁运行管理单位的规定定期检查,进行涂层劣化评定,评定方法依据IS04628。根据漆膜劣化情况,选择合适的维修或重涂方式。
4.4.2维修涂装
维修涂装要求如下:
a)当面漆出现3级以上粉化,且粉化减薄的厚度大于初始厚度的50%,或由于景观要求时, 彻底清洁面涂层后,涂装与原涂层相容的配套面漆(1~2)道;
b)当涂膜处于(2~3)级开裂,或(2~3)级剥落,或(2~3)级起泡,但底涂层完好时,选择相应的中间漆、面漆,进行维修涂装;
c)当涂膜发生Ri2~Ri3锈蚀时,彻底清洁表面,涂装相应中间漆、面漆。
4.4.3重新涂装
重新涂装要求如下:
a)当涂膜发生Ri3以上锈蚀时,彻底的表面处理后涂装相应配套涂层;
b)当涂膜处于3级以上开裂,或3级以上剥落,或3级以上起泡时,如果损坏贯穿整个涂层,
应进行彻底的表面处理后,涂装相应配套涂层。
4.4.4工艺要点
4.4.4.1 根据损坏的面积大小,钢桥外表面可分为以下三种重涂方式:
a)小面积维修涂装。先清理损坏区域周围松散的涂层,延伸至未损坏区域50mm~80mm,并应修成坡口,表面处理至Sa2级或St3级,涂装低表面处理环氧涂料十面漆;
b)中等面积维修涂装。表面处理至Sa2.5级,涂装环氧富锌底漆+环氧(云铁)漆十面漆;
c)整体重新涂装。表面处理至Sa2.5级,按照4.2.1要求的涂装体系进行涂装。
4.4.4.2钢桥内表面维修或重新涂装底漆宜采用适用于低表面处理的环氧底漆,并宜采用浅色高固体分或无溶剂环氧涂料。
4.4.4.3海洋大气腐蚀环境和工业大气腐蚀环境下的旧涂层须采用高压淡水清洁后,再喷砂除锈。
4.4.4.4处于干湿交替区的钢构件,在水位变动情况下涂装时,应选择表面容忍性好的涂料,并能适应潮湿涂装环境的涂层体系;
4.4.4.5处于水下区的钢构件在浸水状态下施工时应选择可水下施工、水下固化的涂层体系。
5试验方法
5.1涂层配套体系
5.1.1耐水性按GB/T 1733的规定进行。
5.1.2耐盐水性按GB/T 9274的规定进行。
5.1.3耐化学品性能按GB/T 9274的规定进行,使用溶液为5%NaOH和5%H2SO.,水溶液。
5.1.4 附着力按GB/T 5210的规定进行。
5.1.5耐盐雾性能按GB/T 1771的规定进行。
5.1.6人工加速老化性能按GB/T 1865的规定进行。
5.1.7涂层体系试验后,漆膜表面缺陷评判按GB/T 1766的规定进行。
5.1.8涂料的试验方法见附录B。
5.2表面处理
5.2.1 除锈等级评判按照GB/T 8923的规定进行。
5.2.2表面粗糙度按照GB/T 13288或GB/T 10610的规定进行。
5.2.3表面油污检查可采用以下两种方法:
a) 粉笔试验法一一适用于非光滑的钢结构表面
对于怀疑有油污污染的区域,用粉笔划一条直线贯穿油污区域。如果在该区域内,粉笔线条变细或变浅,说明该区域可能被油污污染;
b) 醇溶液试验法一一适用于所有钢结构表面
对于怀疑有油污污染的部位,用蘸有异丙醇的脱脂棉球擦拭,并将异丙醇挤入透明的玻璃管中。加入2~3倍的蒸馏水,振荡混合约20min。以相同体积的异丙醇蒸馏水溶液为参照,如果溶液呈混浊状,表明钢结构表面有油污污染。
5.2.4表面灰尘清洁度按GB/T 18570.3的规定进行。
5.2.5表面可溶性氯化物按GB/T 18570.6和GB/T 18570.9的规定进行。
5.3现场涂层
5.3.1 涂层厚度
5.3.1.1 湿膜厚度按GB/T 13452.2的方法6规定进行。
5.3.1.2干膜厚度按GB/T 13452.2的方法5规定进行。
5.3.2涂层附着力
5.3.2.1 涂料涂层附着力按GB/T 9286或GB/T 5210的规定进行。
5.3.2.2锌、铝涂层附着力按GB/T 9793-1997附录A中的栅格试验法规定进行。
6检验规则
6.1 取样
6.1.1 现场取样应使用专用的样品取样罐。确保现场取样罐的清洁,没有灰尘、水等杂质。
10 JT/T 722-2008
6.1.2抽检的产品包装完整,标志清晰。
6.1.3采用电动或气动搅拌装置,确保抽检产品均匀一致。
6.2检验项目
6.2.1涂层性能的检测项目见表8。
6.2.2进场涂料检测项目由监理、施工方及涂料供应商从附录B中所列项目中选定。
6.2.3现场涂层检测项目按照4.3.3执行。
6.3判定原则
6.3.1 涂层性能的检测为型式检验,应由涂料供应商提供国家认可检测机构出具的涂层性能的合格的检测报告。
6.3.2进场涂料检测结果全部符合本标准的要求为合格。检测结果有一项指标不符合要求时,允许对不符合要求的项目进行复验,复验结果仍不符合要求,则判该批产品为不合格。
6.3.3现场涂层检测结果全部符合4.3.3条款为合格。检测结果有一项指标不符合要求时,都应在现场处理至合格后方可进入下道工序。
7安全、卫生和环境保护
7.1 安全、卫生
7.1.1 涂装作业安全、卫生应符合GB 6514、GB/T 7691、GB/T 7692和GB/T 50212的有关规定。
7.1.2涂装作业场所空气中有害物质不超过最高容许浓度。
7.1.3施工现场应远离火源,不允许堆放易燃、易爆和有毒物品。
7.1.4涂料仓库及施工现场场有消防水源、灭火器和消防工器具,并应定期检查。消防道路应畅通。
7.1.5密闭空间涂装作业应使用防爆灯、器具,安装防爆报警装置;作业完成后油漆在空气中的挥发物消散前,严禁电焊修补作业。
7.1.6施工人员应正确穿戴工作服、口罩、防护镜等劳动保护用品。
7.1.7所有电器设备应绝缘良好,临时电线应选用胶皮线,工作结束后应切断电源。
7.1.8工作平台的搭建应符合有关安全规定。高空作业人员应具备高空作业资格。
7.2环境保护
7.2.1 涂料产品的有机挥发物含量(VOC)应符合国家有关法律法规要求。
7.2.2保持施工现场清洁,产生的垃圾等应及时收集并妥善处理。
8验收
8.1 涂层验收可按构件分批次验收。
8.2涂装承包商至少应提交下列验收资料:
——设计文件或设计变更文件;
——涂料出厂合格证和质量检验文件,进场验收记录;
——钢结构表面处理和检验记录;
——涂装施工记录(包括施工过程中对重大技术问题和其它质量检验问题处理记录);
——修补和返工记录;
——其它涉及涂层质量的相关记录。
附录A(规范性附录)
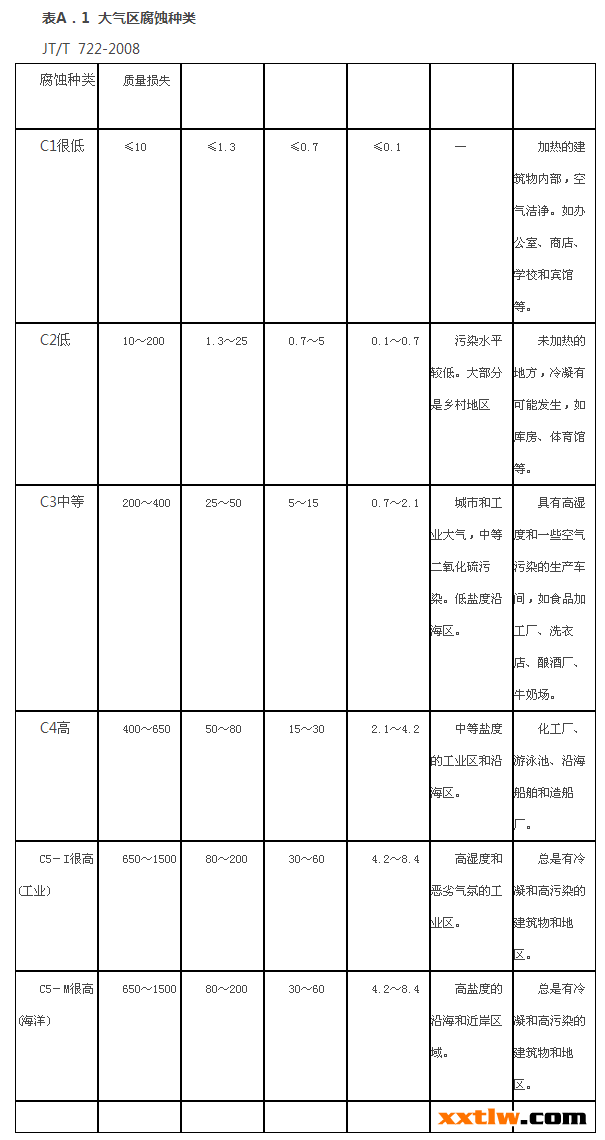
注:在沿海区的炎热、潮湿地带,质量或厚度损失值可能超过C5-M 种类的界限。
A.2浸水区
A.2.1 按水的类型将浸水区腐蚀环境分为两种类型:淡水(Iml),海水或盐水(Im2)。
A.2.2按照浸水部位的位置和状态,将浸水区分为三个区域:
一一水下区:长期浸泡在水下的区域;
一一千湿交替区:由于自然或人为因素水面处于不断变化的区域;
一一浪溅区:由于波浪和飞溅致湿的区域。
A.3埋地区
埋地环境定义为一种腐蚀类型Im3。